Vaporization and Condensation in Compact Heat Exchangers
DOI 10.1615/hedhme.a.000307
3.9.12 Vaporization and condensation in compact heat exchangers
Ralph L. Webb
A. Introduction
Gas processing (liquefaction and separation) in plate-fin brazed aluminum exchangers frequently involves convective condensation and evaporation in the plate-fin channels. Typical geometries used include plain fins, offset-strip fins, and wavy fins. The design theory for calculating the vaporization and condensation coefficients is founded on existing fundamentals of convective condensation and evaporation in channels. The key difference is how the specific brazed aluminum channel geometry affects the heat transfer coefficients.
For automotive evaporators and condensers, a somewhat different channel geometry may be used than in large brazed aluminum for gas processing. However, the fundamentals remain the same. In automotive condensers, the condensation typically occurs in multiport extruded aluminum tubes. Figure 1 shows two extruded aluminum tubes used in "parallel-flow" refrigerant condensers. The top tube is now outdated and is 3 × 16 mm with 0.5 mm wall. The bottom tube is a more advanced 1 × 16 mm with 0.22 mm wall, having 0.55 mm hydraulic diameter.
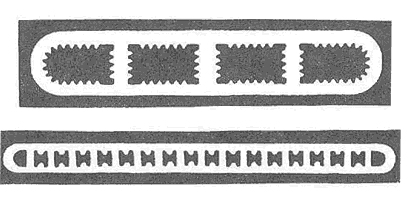
Figure 1 Extruded aluminum tubes used in "parallel-flow" refrigerant condensers: (a) top tube is 3 × 16 mm with 0.5 mm wall; (b) bottom tube is 1 × 16 mm with 0.22 mm wall, having 0.55 mm hydraulic diameter
Readers are referred to Webb and Kim (2005), Chapter 13 for discussion of convective vaporization and Chapter 14 for convective condensation. Hesselgreaves (2000) gives further detail for convective vaporization and convective condensation in compact heat exchanger fin geometries.
... You need a subscriptionOpen in a new tab. to view the full text of the article. If you already have the subscription, please login here